Jewelry Casting Process
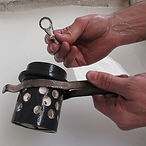
The lost wax jewelry casting process usually starts with a master model of the piece to be recreated.
A rubber molding material is used to create a flexible mold of the master model. A fluid wax is injected into the rubber mold to create the original piece. Once cooled, the wax piece, or pattern, is removed from the rubber mold.
Wax patterns are attached to a wax pole, or sprue. The wax patterns and sprue will eventually create the void in the castable mold that will fill with molten metal. The complete wax assembly of patterns and sprue is referred to as a tree. Each tree may contain a short sprue with a few wax patterns or dozens of patterns around a single sprue.
After preparing the trees, the sprue is placed onto a rubber base and a cylindrical metal flask is secured around the tree. Then a plaster like material, called investment, is prepared to form a slurry. The slurry is poured inside the flasks, around the trees. Once the slurry has hardened, the rubber sprue base is removed and the mold is ready for the wax removal process. The flask is placed into an oven. With a controlled heating cycle, the investment mold is cured and the wax is completely melted from the mold. A hollow void is left in its place, which replicates the wax tree in complete detail.
Molten metal is poured into the sprue opening, filling the void and recreating the original wax tree with a metal replica. Once cooled, the investment can be cleaned from the metal in a water bath. The jewelry pieces can then be cut from the metal sprue and finished to complete the desired cast piece.